Self Cleaning Filters Eliminate Particles
Aug 1996, Pollution Engineering, Cahners Publishing Company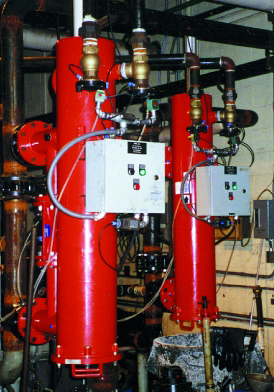
Two 350 gpm automatic water filters were installed vertically, three feet above the floor to save space.
OMC Spruce Pine, Spruce Pine, N.C., is a “lost foam” casting facility for the manufacture of marine engine parts. A styrofoam mold is created in the shape of the desired part and then surrounded with sand. When molten aluminum is poured onto the mold, the metal takes the shape of the part and the foam is burned off.
The plant was experiencing problems with clogging caused by oil-saturated polystyrene beads that found their way into the water used for press hydraulics and machinery cooling. The result was extra maintenance and downtime, compromised product quality and a more difficult waste stream to treat. The plant needed a filtration system that would prevent particle buildup and eliminate clogging. Self-cleaning filters, manufactured by Orival Inc., Englewood, N.J., provided the solution.
“Previously, we were using disposable filters on each of the 11 presses,” explains OMC maintenance manager and environmental coordinator, Gary Pipes. “Filter cartridges had to be replaced every week, sometimes more frequently, at a cost of $20 per press. After one year, the filter housing also needed to be replaced, so it was a good time for us to look at other options.”
OMC initially installed a single Orival filter to screen the water used for cooling and hydraulics. “I was skeptical of the Orival claims,” Pipes confesses, “so we installed the filter without removing the housing for the old system, in case we needed something to fall back on. But the new filter did a better job than the disposable filters, and the project cost us about the same as what we were spending annually to replace filter cartridges.”
“The new filter did a better job than the disposable filters, and the project cost us about the same as what we were spending annually to replace filter cartridges.”
Pleased with the results of the first filter, OMC installed a second Orival filter, this one in the recirculation loop that takes water from the presses to the sump.
The Orival filters met OMC's list of criteria. Most importantly was the ability to remove particles of any specific gravity, especially lighter than water. “The styrofoam beads change specific gravity the longer they remain in the system,” Pipes explains. At first they float, but later become like gravel, sinking to the bottom. Beads are now filtered out and can be landfilled rather than creating headaches for the local waste water treatment plant.
The Orival filters are retrofittable with various screen sizes, which allowed OMC to experiment to find the proper size. “We started with an 80 micron fine screen, which we thought would be necessary to eliminate clogging. Due to 'caking action' however, the screens filter smaller particles and even oil. We eventually settled on a 400- micron screen, which allows a higher flow rate through the system. Once the optimum size was found, the screens have never needed to be replaced.”
The Orival filters are not affected by oil in the water, whereas the disposable filters clogged with oil more quickly and had to be replaced. “The new filters are self cleaning,” says Pipes, “and the cleaning cycle takes so little time, we remain online. We never need to use the automatic built-in bypass.”
“Since installing the Orival filters almost two years ago, our clogging problems have gone away,” says Pipes. “The new filters are basically maintenance free.”