If it Glitters it May Be Gold
Apr 2007, Dr. Marcus N. Allhands, PE, VP Business Development Orival, Inc.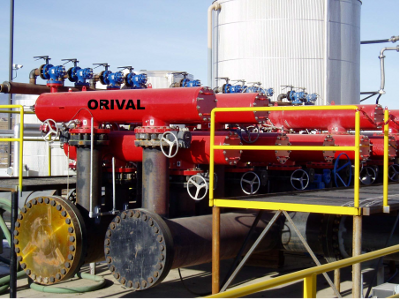
Figure 1. Orival filtration system
What do gold and automatic self-cleaning screen filters have to do with one another? The tale below tells of this unusual yet necessary relationship.
Well into prehistory man has marveled at the sight of gold. It had no sustaining significance since it could not be eaten or worn. But its luster, durability and shear beauty were mystifying. For nearly 4000 years gold has been a standard for monetary measure. Even today speculators invest in its stability above the economy of all world powers.
Most surface, or alluvial, gold has been found in the US by 49ers and their immediate successors. Today’s gold mining operations must go underground and may be open pit or underground shafts and tunnels. Either way, ore is extracted and processed by the method most appropriate for the ore grade and composition. The very simple process of dissolving gold in cyanide, using activated carbon to adsorb the gold out of solution and then chemically stripping the gold from the carbon and precipitating by electrolysis is used for low-grade oxide ores. This process is called the leaching circuit. High-grade ores, though higher in gold concentration, require more extensive processing depending upon ore type. Ore containing carbon and sulfide is called refractory ore and must be heated to 1000°F to burn off the carbon and sulfide. The remaining rock is then processed in the leaching circuit. Sulfide refractory ore contains no carbon so must be oxidized in an autoclave under extreme heat and pressure where the sulfide is removed before the ore heads to the leaching circuit. High-grade oxide ores, like low-grade ore, head directly to the leaching circuit. The resulting gold extract is about 90% pure. This impure gold is poured into doré bars and sent to a refinery.
“Since the first filters were installed in October 2004, they have performed reliably. Periodic internal and external inspections have shown no problems or weaknesses.”
According to Natalie Deringer, Senior Metallurgical Engineer for Barrick Gold Corporation, Cortez Mine specialists discovered the Nevada Pipeline Gold Deposit in the early 1990’s. By 1997 a mill for recovering gold from the Pipeline was up and running. This was the start of something big, over 9,000,000 ounces big. Generally, if the gold content of the ore is 0-0.002% the shiny metal is not economically recoverable. Low grade ore containing 0.03-0.09% gold goes directly to “heap leach” which begins the leaching circuit. Ore containing >0.09% gold begins its process at the mill. The open pit Cortez Mine has all three ore types.
The “heap leach” process begins by laying out a 50-80 mil thick blanket of plastic film on an area of graded ground about 1 mile wide and 2 miles long. (If I haven’t had your attention, the shear size of this process should grab it now.) Perforated drain pipe is laid out in evenly spaced parallel rows along the two mile length of plastic. Next a 2’ deep layer of rounded gravel is placed on top of the plastic burying the drain pipes beneath. Crushed ore is dumped on top of the gravel layer in heaps forming a flat topped ridge (trapezoidal cross section) about twenty feet deep. Irrigation equipment (having no aluminum or brass) sprays a dilute aqueous cyanide solution on the heap continuously saturating the heap and leaching gold from the ore. When nearly all the gold is leached from the ore another twenty foot layer of virgin ore is added to the top of the heap and saturated with cyanide solution. This continues until eventually the heap will approach the status of a two mile long hill 200 feet high and nearly a mile wide at its base. When all the gold is leached from the heap, a clay layer is added to cap off the heap and then top soil is added to the face and trees planted forming part of the permanent landscape. This total process may take years to complete.
The leachate (cyanide solution that has passed through the depth of the heap) carrying gold in solution passes through the gravel layer and into the perforated drain pipes. These pipes discharge their contents into the “pregnant” pond. Gold laden solution from this pond goes to granulated activated carbon (GAC) tanks where the gold is adsorbed onto the carbon and the cyanide leaches through the carbon and is discharged to the “barren” pond. When the GAC can hold no more gold, it is trucked to the elution circuit at the mill where the carbon is first acid washed. Next the gold laden GAC is stripped of its payload by a thermo-chemical process using sodium hydroxide (NaOH) and sodium cyanide (NaCN) at a temperature of 270°F. The gold is now back into solution and drained from the GAC bed in to the pregnant tank. A very large DC current is passed though this solution and through electrolysis the gold precipitates out forming sludge in the bottom of the pregnant tank. This sludge is dried and then melted into 87-90% pure gold doré bars which are taken to a refinery to produce 99.99% pure gold bars.
Where do the filters come into the picture? We left the aqueous cyanide solution above, in the barren pond after traveling through the heap leach, the pregnant pond and the GAC tanks. This solution is fortified with additional cyanide (a by-product from the making of nylon) to replace any lost material and recycled back to the heap leach pile to extract more gold. However, particulates in the solution have a nasty habit of plugging the sprinklers and nozzles on the heap leach pile greatly decreasing the efficiency of the process and requiring extensive man-hours under hazardous conditions to unplug nozzles. The solution is to add an additional step to the procedure. A specialized filtration system is located between the barren pond and the sprinkler system to remove the problem particulates. Since the process must maintain a pumping rate of 20,000 gpm at 300 psi 24/7 with no break for holidays, the filtration system has to be dependable under very strenuous conditions and made of materials compatible with cyanide. An Orival automatic self-cleaning filtration system was chosen for this application (Figure 1). A bank of ten Orival Model OR-12-PS-HP automatic filters were installed on an Orival designed and manufactured manifold. Each filter contains a rugged 100 micron (150 mesh) stainless steel weave-wire screen. These specially designed filters contain no brass (brass is non-compatible with cyanide) and are rated for high pressure applications. Producing high value products requires high quality equipment. Natalie Deringer testified, “Since the first filters were installed in October 2004, they have performed reliably. Periodic internal and external inspections have shown no problems or weaknesses.”