Filtering Metallics at Midland
Mar 1994, George W. Hess, National Editor, Newsteel, Chilton Publications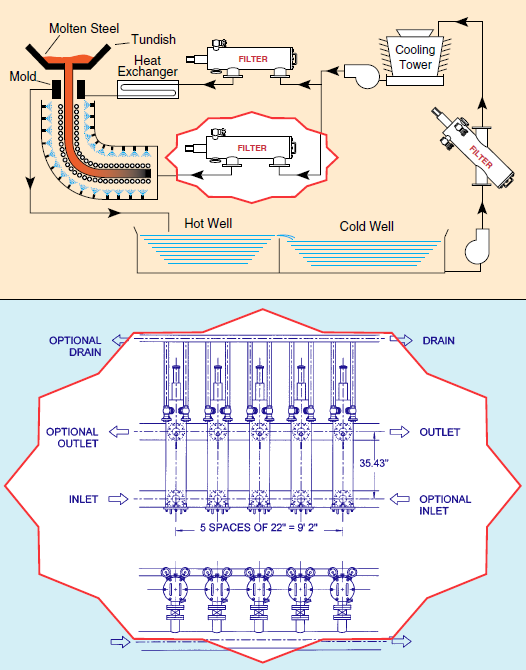
For schematics: Filters at J&L Specialty, upstream of the caster, remove dirt particles from recycled cooled water; this saves the spray nozzles from clogging.
Producing steel that's consistently clean inside and out—free of inclusions and surface blemishes, that is—from heat to heat is a daunting task. J&L Specialty Products' mill at Midland, Pa., is ensuring high quality and cutting downtime by an improvement of the cooling-water system serving its continuous slab caster.
As in many steel plants, the process water at Midland is collected and recycled through a cooling tower. The water is sprayed directly on the continuously cast slab below the mold to hasten solidification; it can pick up metallics that clog spray nozzles or erode their outlets. The result: an uneven flow of water. This can degrade product quality and requires filtering to keep the water free of contaminants.
“There are two primary sources of dirt,” says John Zurchin, a J&L process control engineer. “Scale and iron oxide are normal byproducts of the continuous casting process. Airborne particles, sand, silt, algae, and microbiological growth are collected by open surfaces, such as the cooling tower and its hot and cold wells. Oil is always present.”
The filters, supplied by Orival, clean themselves automatically and are unaffected by oil.
Midland once used baskettype strainers to remove dirt from its cooling water. But maintaining the strainers added cost and caused downtime. “We decided to replace the basket strainers as part of an overall upgrading of the cooling-water handling system,” Zurchin says.
J&L Specialty now uses a line-pressure-powered, self-cleaning unit that filters particles down to micron sizes of any specific gravity, even those lighter than water. The filters, supplied by Orival Inc. (Englewood, N.J.), clean themselves automatically and are unaffected by oil. In two years of use, they have cut maintenance downtime and costs greatly, Zurchin says.
The five filters at Midland provide an uninterrupted flow of 1,300 gallons per minute at 225 pounds per square inch. Each is equipped with a 474-square-inch, 100-micron stainless-steel screen and an 8-inch automatic bypass.