Full-Stream Cooling Tower Filtration
Mar 2013, Dr. Marcus N. Allhands, PE, VP Business Development Orival, Inc.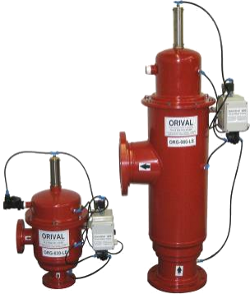
Figure 1. ORIVAL ORG Series Automatic Self-Cleaning Filters
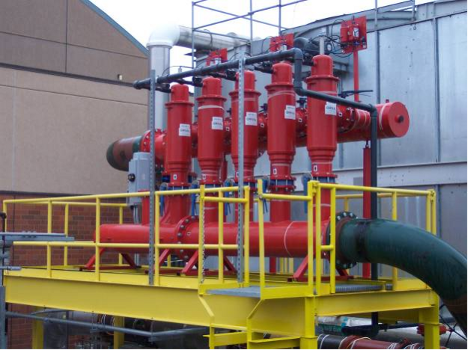
Figure 2. ORIVAL Five-Filter System
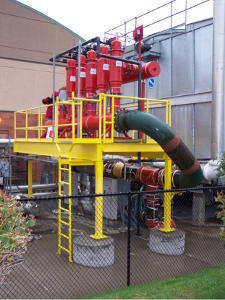
Figure 3. Filtration System Layout
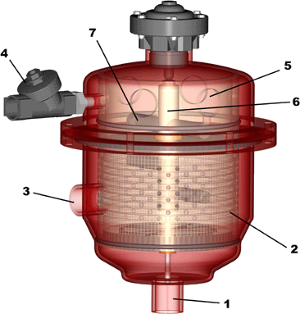
Figure 4. ORG Filter Cut-A-Way
Introduction
Water chemistry is routinely addressed in cooling systems. Scale formation, corrosion and biological growth are just some of the activities that can be abated by proper use of chemical additives. Foreign matter in the form of suspended solids though, is too often overlooked in the design stage. Control of this physical problem is generally addressed sometime after operation has begun when heat transfer problems arise.
Problem
A large Midwest pharmaceutical plant for animal vaccines and medications caters to cattle, swine, equine and companion animals such as cats and dogs. Highly sophisticated processes are utilized to produce pharmaceuticals; and cooling is a very important component of these processes. In-plant cooling means cooling towers and the twin-cell cooling tower at this site acts as a wet air scrubber trying to clean the atmosphere of the entire agricultural community. Plant engineers soon discovered that the small 90 m3/hr (400 USgpm) side-stream four-bag filtration system on their 1200 m3/hr (5300 USgpm) cooling tower system did not provide the protection they needed for heat exchangers, condensers and vessel cooling jackets scattered throughout their facility in addition to an 800 ton chiller. Plus, changing the bags based on a differential pressure alarm was labor intensive and not always attended to in a timely manner.
Their Capital Projects Engineering Department began looking for a full-stream filtration system to filter the 1200 m3/hr (5300 USgpm) flow with a 275–345 kPa (40-50 psi) operating pressure down to 100 microns. Space on the outdoor concrete pad was very limited. To make matters worse, the concrete pad’s surface was partially flat and partially inclined. Two pumps moved water from the cooling tower basin up to a 450 mm (18-inch) header located about two meters above the concrete pad. A third pump was to be added when the filtration system was installed to provide a backup.
Designing a Solution
When designing mechanical filtration equipment one must provide adequate hydraulic capacity maintaining reasonable velocities through the inlet and outlet flanges to minimize static pressure losses, taking into account streamline turbulence caused by internal filter structures and components and numerous changes in direction of fluid flow. However, a bigger design criterion is sufficient screen area to handle water quality conditions. As at most Midwest settings, insects, sand, leaves, dust, pollen, cottonwood seeds and algae as well as man-made debris such as paper, cups and grass clippings influence the water quality greatly. The filter flux must be of appropriate value to meet the specific conditions of filtration degree, TSS loading and type of solids. Filter flux is defined as the flow rate per unit area of screen media, i.e. m3/hr/cm2 (gpm/in2) of usable screen surface. A filter model with small footprint and large screen area was chosen to meet the specific demands of this application (see Figure 1). Five Orival Model ORG-080-LS automatic self-cleaning filters were mounted on a 400 mm (16-inch) manifold that included a blind flange so that a sixth filter could be added at a later date should it become necessary (see Figure 2). A 400 mm (16-inch) pneumatically actuated by-pass valve was incorporated into the manifold system to be opened automatically should the filtration system controller sense a fault in the filtration process. The controller also has a set of dry contacts for connecting an alarm system for fault situations. A 200 mm (8-inch) manual butterfly valve was located at each filter inlet and outlet to allow the isolation of any individual filter for maintenance or repairs. The filters were pre-mounted on the manifold system before shipping to the site but the system had to be broken in half for truck shipment.
Normally the hydraulic piston used to move the self-cleaning mechanism (dirt collector) linearly inside each filter and the rinse valve are operated by the water and pressure in the system. However, these filters would possibly operate during the winter months when freezing would be a problem. Therefore, available industrial pressurized air is used to pneumatically operate the pistons and rinse valves. The piston and rinse valve actuator on each filter are filled with a glycol mixture that connects to an accumulator tank. This tank is partially filled with the glycol mixture and then the tank is pressurized with the industrial air supply. A solenoid valve bleeds air from the tank lowering pressure; thus, allowing the rinse valve to open and the piston to operate when signaled by the controller to initiate a cleaning cycle. Cleaning cycles automatically occur when a 0.5 kg/cm2 (7 psi) pressure differential develops across the inlet and outlet manifolds or when a preset timer lapses. Filter No. 1 goes through its 15 second cleaning cycle and then Filter No. 2 and so on sequentially until all five filters have cleaned themselves. Each filter remains on-line at all times with no disruption of the filtration process.
A design/build firm installed the filtration system mounting the entire package about 3.5 m (12 feet) above ground level on a mezzanine built on-site (see Figure 3). This overcame the uneven concrete pad problem and put the filters in line with where the cooling water enters the building. Each filter is equipped with a liquid-filled pressure gauge and a 3-way selector valve. This allows the inlet pressure, outlet pressure and rinse chamber pressure to be conveniently observed with one gauge on each filter unit eliminating variations between gauges. Using these pressures allows one to run a number of diagnostics on each filter.
Results
Prudent use of appropriate chemical additives, routine blowdown and proper filtration has resulted in exemplary performance with no maintenance issues or process interruptions.
Exemplary performance with no maintenance issues or process interruptions.
Filter Operation
Referring to Figure 4, dirty water enters the inlet (1), where it goes into the center of the cylindrical fine screen element (2). The water then passes through the fine screen from the inside out and exits the outlet (3). The unwanted solids accumulate on the inner surface of the fine screen, creating a pressure differential across the screen element. Once the pressure differential reaches a preset value (normally 7-psi), a rinse cycle is activated when the factory supplied control system opens the rinse valve (4) to an atmospheric drain. As a result, the pressure drops in the hydraulic motor chamber (5) and dirt collector assembly (6). The pressure drop causes water to backflush through the screen in an area about the size of a dime (about ½” diameter circle) at the nozzle openings which are located very close to the inner screen surface. This high velocity backflush stream pulls the dirt off the screen, similar to a vacuum cleaner. The backwash water is carried through the collector and ejected out of the holes in the hydraulic motor (7). The water being ejected out of the hydraulic motor causes the collector to rotate, similar to an old-style lawn sprinkler. In addition, pressure is released from the hydraulic piston (8) located at the top of the filter causing the collector assembly to slowly move upward. This combination of rotational and linear movements ensures that the entire screen area is cleaned each cycle. The cleaning cycle of the smaller ORG filters takes less than 10 seconds, discharging as little as 3 gallons per cleaning cycle while larger filter models like those used in this project can take up to 15 seconds to clean utilizing about 11 gallons of water.